How NaviSuite software is laying the way for unmanned, automated pipeline inspections
Taking on the challenge of autonomous pipeline inspections
Increasingly, pipeline survey companies seek to reduce manual intervention. The goal is to reach the point where surveys can be performed by an entirely autonomous system – meaning with no manual intervention at all.
This is because autonomous surveys provide a sea of benefits. Not only do they increase efficiency and reduce costs (in the form of vessel time and man hours), but the data retrieved from autonomous surveys provides more standardised output and hence more objective and consistent results! Because of the increased systematic approach compared to human intervention and evaluation, it makes faultfinding and correction easier. Additionally, it minimises the environmental impacts of a survey thanks to the smaller vessels, increased survey efficiency and less travel around the world for the involved personnel.
Embarking on a development project
With these benefits in mind, EIVA joined in a development project from 2018–2019, with several innovative companies: Swire Seabed, Kongsberg and SEA-KIT. Together, we worked to develop an autonomous pipeline survey system, with the EIVA team working on the software solutions needed.
The novel set up, designed during the project, was tested out during an unmanned commercial inspection of 175 km of pipe for Equinor. The setup involved an unmanned surface vehicle (USV) and autonomous underwater vehicle (AUV). The USV transported the AUV to the defined starting location. From there, the AUV travelled along the pipeline, collecting and processing data until it was recovered by the USV. For the inspection, the project team used a HUGIN AUV and SEA-KIT Maxlimer USV.
During this project, EIVA developed the groundwork of software support for autonomous inspections. In this article, we dive into which software capabilities this project revealed to be necessary for enabling autonomous inspections – and how we are developing them in NaviSuite! These include automatic re-tasking workflows, onboard eventing and navigation aiding. EIVA’s software development benefited greatly from real-life experience in pilot tests and teamwork with the other companies in this project.
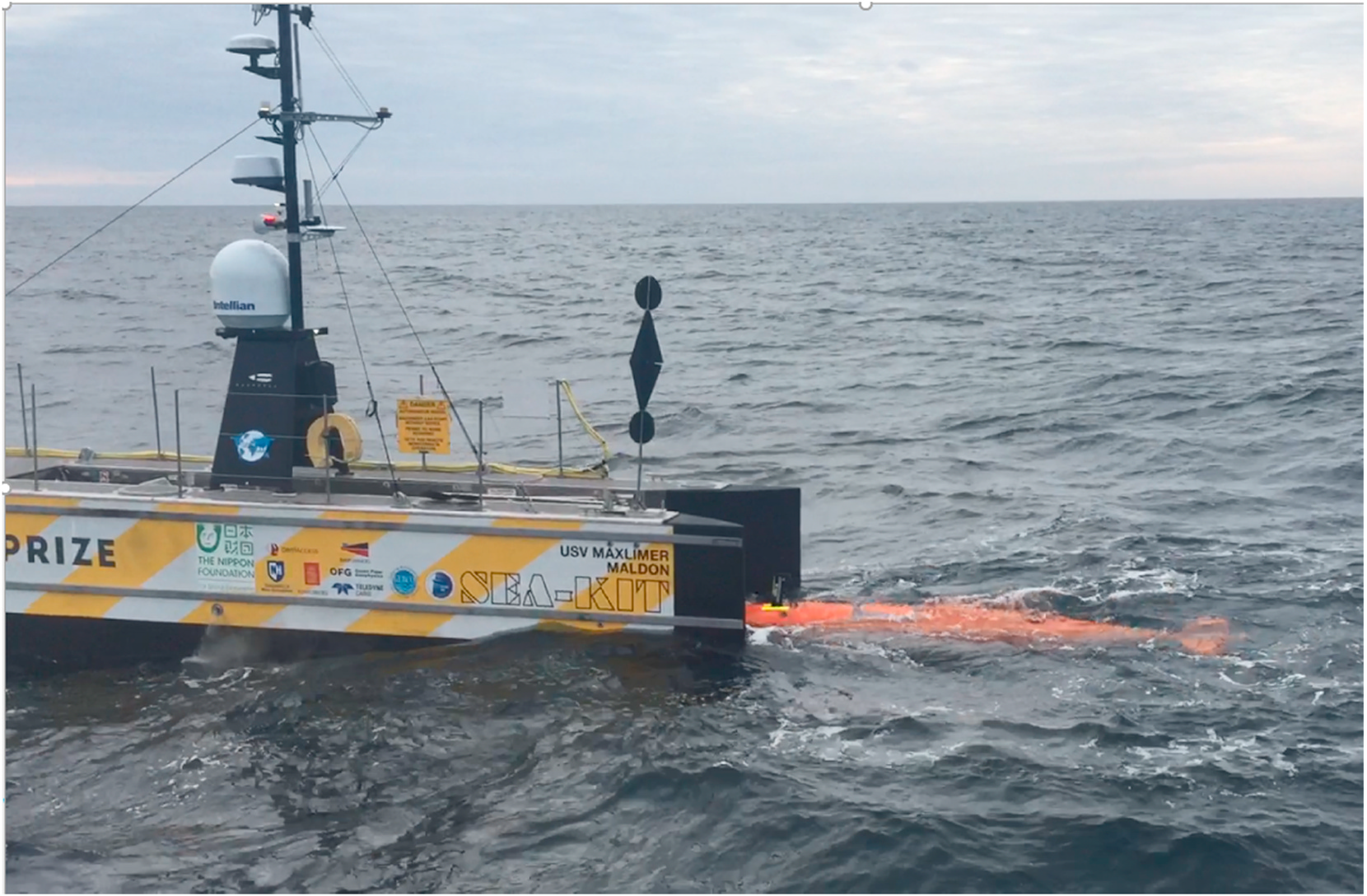
Sea-Kit Maxlimer recovering the HUGIN AUV – Image courtesy of Al Rumson and featured in this article
EIVA’s part: Software solutions sailing us into the future
For the survey to be completely autonomous, an AUV must react to its surroundings automatically –for example by retasking and repositioning the AUV based on the data it collects. To facilitate this, the software onboard the AUV must be able to automatically collect, process and analyse data about the pipeline in real time during a dive. NaviSuite is a software solution capable of supporting operations from collection and processing to analysis, making it up to the task.
Deep learning facilitates onboard data analysis and navigation aiding
The first step towards the AUV automatically reacting to the data it collects, is to automatically analyse that data. For this, we used NaviSuite Deep Learning, which is available as an upgrade to our pipeline inspection software bundle, NaviSuite Nardoa. This software solution is designed for automatic eventing. It can currently identify over 20 different object types along a pipeline, including the top of pipe, anodes, field joints, damages, boulders, and debris. Our simulator tests have shown that using NaviSuite Deep Learning to automate analysis rather than eventing manually saves significant amounts of time.
During the pilot tests, this automatic eventing had to be run offline post-inspection – but by the end of the project, the capability to run automatic eventing onboard the AUV in real time was added to NaviSuite Deep Learning. This was a vitally important step towards supporting autonomous surveys because it makes it possible to use the eventing outputs for retasking, sending alarms and navigation aiding – which we will dive in to in the next section.
In order for NaviSuite Deep Learning to be used onboard an AUV during dives, the AUV must be equipped with an onboard computer. This is one of three ways to use NaviSuite Deep Learning, and the method which works for autonomous surveys.

Watch this pipeline survey video, in which NaviSuite Deep Learning is used to segment object types by colour
The next step was to take the events, which are registered automatically with NaviSuite Deep Learning, and use them for navigation aiding. One of the object types easily registered by NaviSuite Deep Learning is the anodes along a pipe. During the project, we refined a navigation aiding method based on tracking the anodes. Since anodes occur at regular intervals, it is possible to compare the expected and observed positions of detected anodes. Through this comparison, this navigation method can tell how the AUV should be repositioned to follow the pipeline’s real, observed position rather than simply following the expected position.
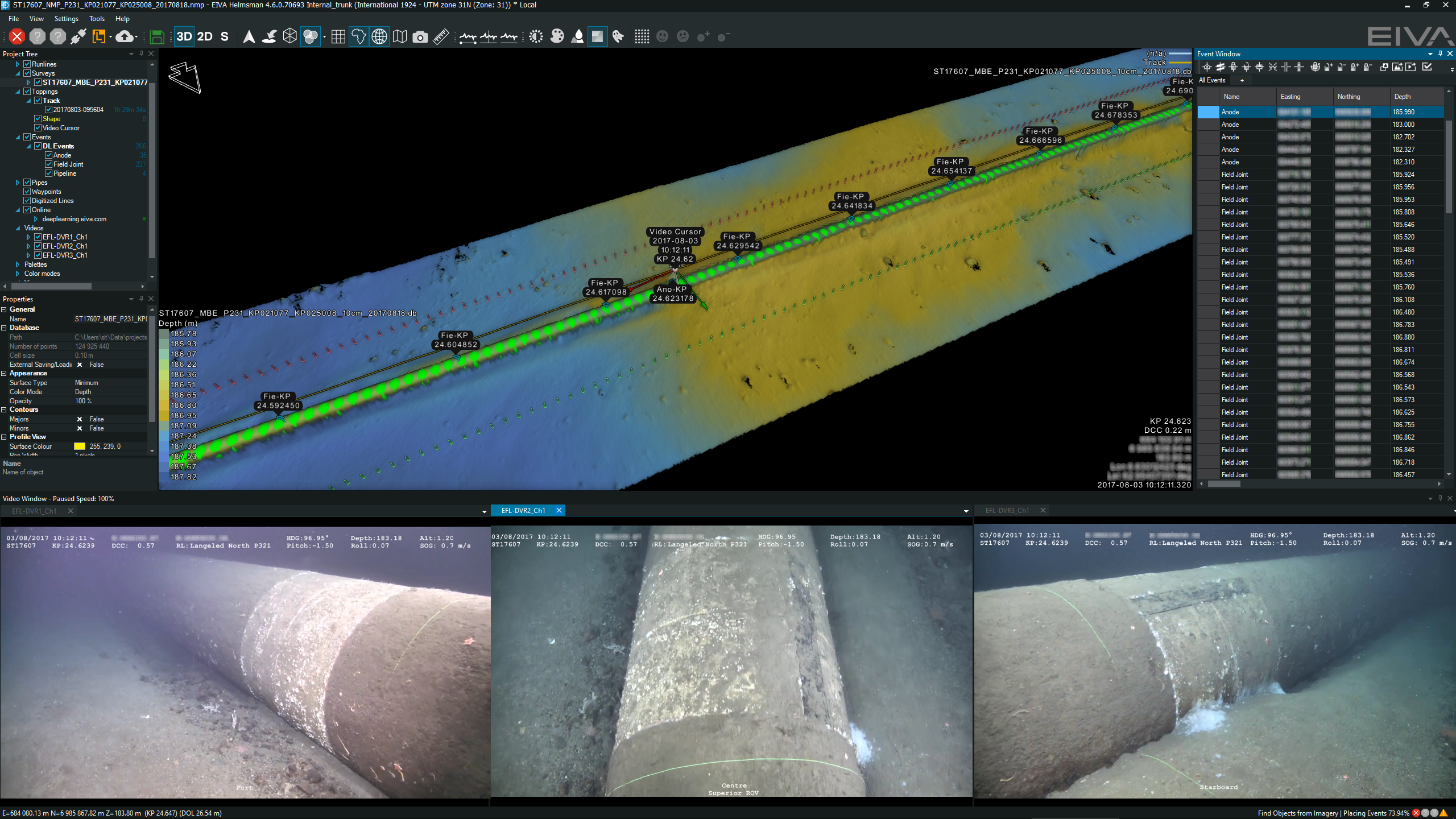
Events such as anodes and field joints are automatically registered with NaviSuite Deep Learning, as you can see in the Event Window (right)
Workflows are the essence of automation
In addition to navigation aiding, we also wanted to be able to use the analysed data to re-task the AUV. Retasking is important if something unexpected occurs. For example, if the data analysis stopped registering the pipeline, the AUV should be re-tasked instead of continuing to scan the wrong area. For example, it could re-run sections of pipeline from the point where navigation has been lost or camera visibility has been bad, for example due to a school of fish passing. This helps ensure full coverage during the survey.
For this, the design of a data workflow was essential. We used our software tool NaviSuite Workflow Manager, which excels at automating repetitive tasks to help customers save time when working in NaviEdit and NaviModel, our subsea data editing and visualisation software solutions. We equipped the AUV with a second onboard computer, on which we could test out the workflows needed.
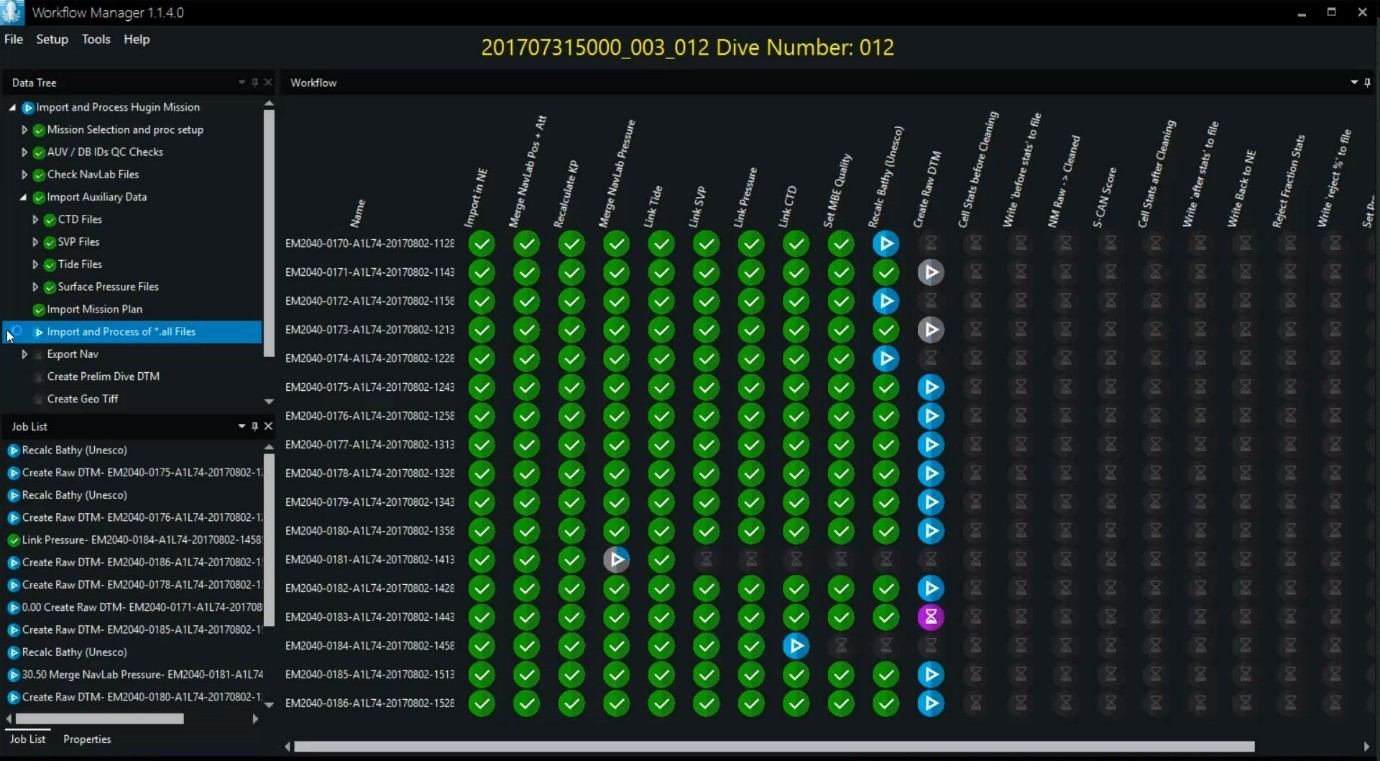
Check out NaviSuite Workflow Manager in action
The retasking workflow was based on feeding the data, which was analysed during AUV dives, back to onshore operators, in the form of alarms and text strings. These alarms could be triggered by specific conditions, such as poor camera visibility, inadequate data coverage, missing sensor inputs and the pipeline not being detected.
Regardless of whether you are performing autonomous operations or not, NaviSuite Workflow Manager saves time during operations as it facilitates onboard processing. By defining the processing workflow, tasks such as data cleaning, quality checking and even eventing can be performed automatically during the dive. So, when the AUV surfaces, there are only a few steps left before the final delivery is ready.
The result is the future of autonomous pipeline inspections
This developmental project was cut short by the unexpected closure of Swire Seabed in early 2020, but not before helping to lay the groundwork for the future of unmanned pipeline inspections! EIVA made huge progress developing automatic data analysis, the necessary workflows for retasking, including alarm generation, QC and eventing, and we refined our navigation aiding method. Many of the software tools we used for this project are available in our software bundle for pipeline & cable route inspections, NaviSuite Nardoa.
Due to the unexpected end of the project, EIVA did not get the opportunity to test out all the capabilities developed during the project on a real inspection, however we see many more opportunities to come… The brave blue world of unmanned inspections is on the horizon and the EIVA crew is looking forward to sailing you there with our software. We can assure you that the journey doesn’t end with this project – there are several other autonomous survey projects with wind in their sails, which we are working on together with various customers and partners in different fields.
For example, we are working on a project with Eelume, for whom our software is providing mission planning, onboard data processing and autonomous navigation aids. We are also involved in the development of Ocean Infinity’s Armada fleet – a whole fleet of USVs, ROVs and AUVs for ocean surveys. Stay tuned for more info on the Armada fleet project coming to the EIVA log.
For news on more articles like this, as well as training courses, webinars and new software and hardware solutions, follow us on social media or subscribe to our newsletter.
Want to help us test our solutions?
Initial test development doesn’t always turn out as expected following the simulation tests – making opportunities for practical testing like this essential. It is important to EIVA that the functionality and user experience of our systems and software meet our customers’ expectations. This is why we often work closely together with our customers to develop software solutions tailored to their needs and test our new tools in the field.
Products in play
NaviSuite Workflow Manager
Configurable workflow process automation tool for subsea survey data processingNaviSuite Deep Learning
Image recognition toolbox for automatic eventingNaviSuite Nardoa
3D software bundle for acquisition and processing of data during subsea pipeline and cable route inspections
Facts and figures
This project was a partnership between Swire Seabed, EIVA, Kongsberg and SEA-KIT
Over the course of the developmental project, seven of Equinor’s pipelines, with a combined length of over 350 km were inspected